Bigger is Not Always Better Says Water Jetting Stalwart
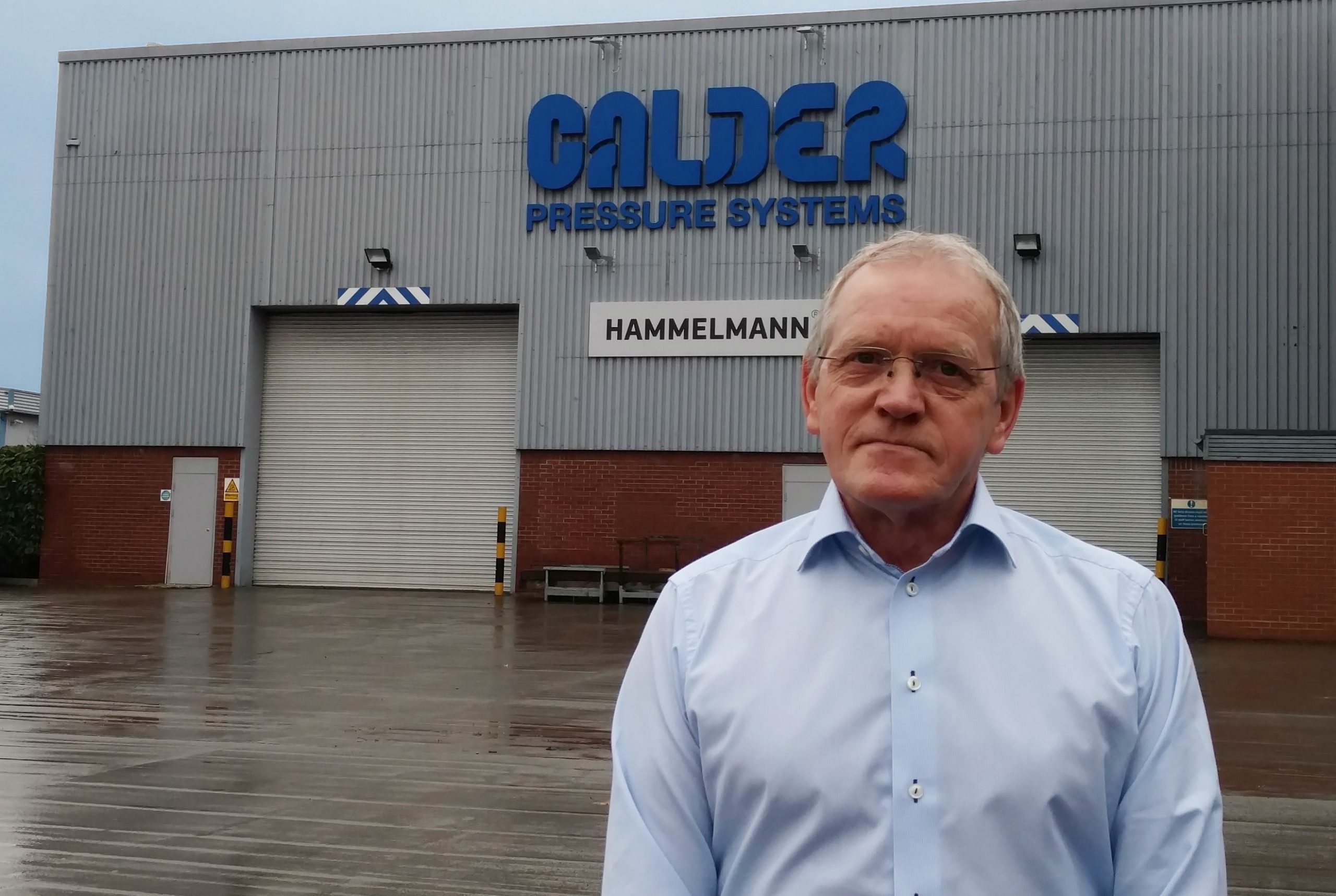
Whatever job needs to be done in the water jetting industry, Billy Campbell must have done it.
In a career spanning five decades, he has worked as a drainage engineer, owned his own drainage business, worked for rental businesses and equipment manufacturers and continues to help pioneer cutting edge water jetting technologies.
Since the late 1970s, he has seen operational water jetting pressures rise from 8,000psi (550bar) to 60,000psi (4,138bar) as new jetting systems and applications have grown in number in equal measure.
Water jetting mantra
As the industry raced ahead, building ever larger pumps, capable of ever larger pressures and water flows, Billy succeeded with a simple mantra – bigger is not always better.
Billy agreed to share his thoughts on water jetting to help the WJA mark its 40th anniversary. The association was founded, at a meeting of contractors in Birmingham, on 9th October 1980.
“Everywhere you looked, people wanted to buy the largest possible water jetting pumps because they thought more power meant better performance,” explains Billy, Industrial Pump Sales Manager with Calder.
“But I quickly realised that was usually not the case. People were over-specifying the equipment. Often, they’d get better operational outcomes from pumps with similar pressures but lower flow rates.
“That meant using less expensive pumps, with more tried and tested technology, running them at less power, so they lasted longer and didn’t break down as often, and using less water, making it operationally easier.”

WJA training
A key factor in the equation was often the training of the operatives, one of several reasons why Billy champions the work of the Water Jetting Association, the trade organisation for the UK water jetting industry.
“The training and capability of water jetting operatives has a big influence on operational effectiveness and safety, which is why the work of the WJA has been so important over the years in terms of setting clear standards, backed by its codes of practice.
“Having the right skills and experience greatly helps operatives and managers make the right decisions about the equipment they use and how they use it and structured training is part of that equation.”
Water jetting educator
Billy’s highly effective sales technique as a water jetting educator has been put to the test across the UK and internationally. In fact, he has been on the go all his life.
As a child he lived around the world, in the Caribbean, Mexico and Africa while has father travelled the globe working as a factory engineer.
Billy had been about to join the Army when, at the last moment, he took a job as a drainage engineer for Strathclyde Regional Council. That led, via Dyno-Rod in Hull, to him setting up his own business, Rescue Jets, in 1980.
He then sold the business and became a contracts manager for an industrial cleaning company which led to his involvement in the early development of abrasive cold cutting. Even Red Adair, the famed American oil well firefighter came over to look at the technology.
Middle East success
Next came a move into working for a manufacturer, Neolith Pumps. After proving himself as a branch manager he was posted to Dubai to support Neolith’s Middle East operation.
Billy helped manage the operation which supplied pumps to the growing industrial enterprises across the Gulf States but had been struggling. Billy was tasked with increasing sales and rentals.
“They were using a lot of water jetting equipment, especially in the desalination plants, but a lot of it was old and the operatives weren’t trained,” said Billy.
“We offered to repair their units, then we could demonstrate they would do much better with more modern pumps, with similar operating pressures but lower output flows. We trained the operatives up to WJA standards, and transformed their performance.”
When Billy returned to the UK, he continued to make best use of this ability of both sell to and educate his customers, always seeking to supply the right equipment and technology.
Ultra-high jetting
In the early 1990s, he helped pioneer the use of ultra-high pressure water jetting for land-based applications. It had previously been used mainly off-shore.
This led him to applying the latest water jetting technologies across many sectors, including the nuclear, off-shore oil, petrochemicals and construction industries.
One project was to set up trials and demonstrations for English Heritage to show how ultra high pressure water jetting could be used for large scale surface preparation during the building of the Eurostar terminal at St Pancras Station in London. He went on to manage those operations for the next six years.
Maintaining standards
Since joining Calder, a WJA member, in 2018, Billy has lost none of his vim and enthusiasm for water jetting, as the company works at the forefront of latest technologies, including semi-automated and automated systems.
“I supposed I’ve seen and been involved in a lot of revolutions and what people call robotic water jetting is the latest, though it has been around for quite some time,” says Billy. “It’s good for lots of reasons, not least safety.
“Automation doesn’t mean dumbing down. Operatives still need to be in control, so they still need to understand water jetting, so they will need to be trained to WJA standards.
“As technology changes, the WJA changes to stay relevant. Maybe that’s my strength too. I’ve stayed relevant and I’m happy with that.”