From a Mole to a Koala – The Global Journey of Water Jetting Pioneers
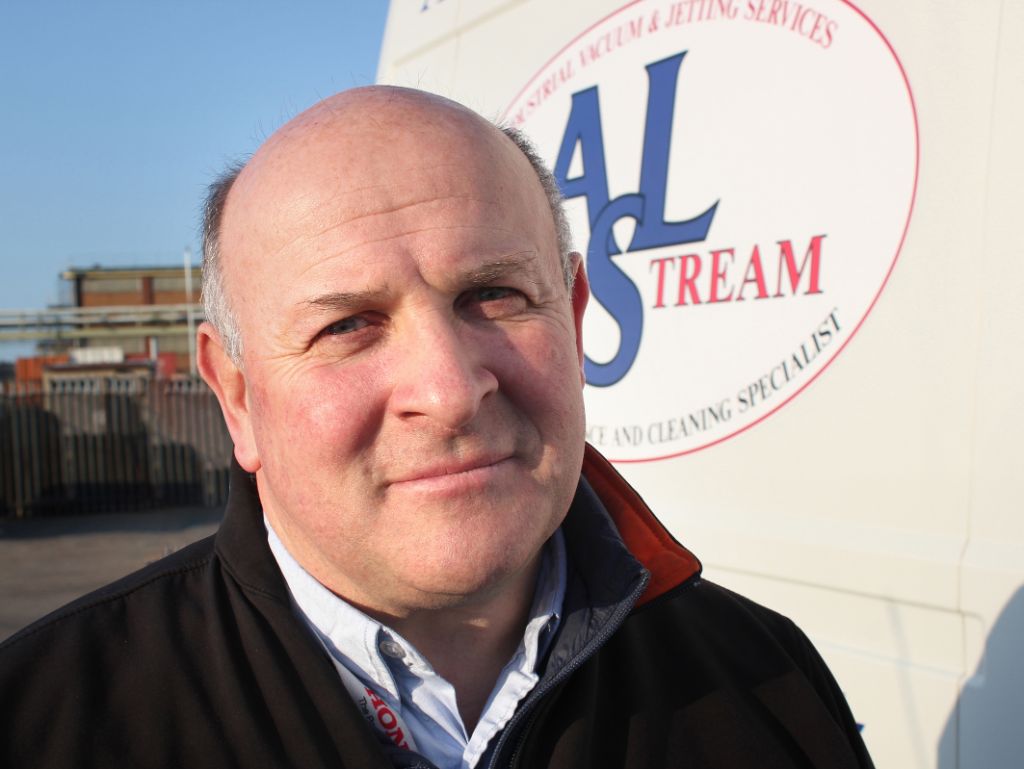
It’s not often nowadays that someone can say they have been involved in an industry man and boy. But that’s true of Richard Walton.
He is the third generation of a family that has been synonymous with the water jetting in the UK – and he did become steeped in the industry as a young boy.
Richard is the Engineering Director of ASL PowerStream, part of ASL Group, whose services include water jetting contracting, heat exchanger manufacturer, and water jetting training.
He talked about his family’s close association with water jetting to help mark the 40th anniversary of the Water Jetting Association, founded in October 1980.

Say cheers to innovation
Richard Walton is the grandson of SR Walton, founder of the Walton Mole company. SR had been a senior engineer at the Winterschladen Brewery in Middlesbrough in the 1930s and 1940s.
One of the brewery’s biggest problems was the build-up of waste, called ‘cake’, in pipes that might taint the brew or cause lengthy shutdowns while the pipework was stripped and cleaned by hand.
His solution was to design and build a mole, a device that could be inserted into pipes and – under the pressure of the liquid – travel along their length, pushing the cake in front of itself as it went.
From that moment on, pipes could be cleaned in situ, without time-consuming shutdowns. It was a gamechanger. The device was so successful SR Walton created the Walton Mole company to manufacture it for other breweries.

Pioneers of water jetting
“The Walton Mole was so successful during the 1940s and 1950s that it was sold to breweries all over the UK,” Richard Walton said. “The company was still servicing Walton Moles into the 1980s.
“Water jetting was just starting in the UK after World War Two, to support the petro-chemical industry which was being established on Teesside and indeed nationally.
“ICI approached my granddad and father, Douglas, who joined the company from Dorman Long in 1962, asking if they could provide water jetting as a contractor, which is how we got started.
“Almost straight away, there was massive demand for water jetting. The only other way to clean heat exchanger tubes at the time was by drilling them out, a process that was taking weeks. Walton Mole could do it in a matter of hours.
“In the 1960s, they had 12 to 14 months of work on the books from the likes of BP, Shell and ESSO, as well as the day-to-day operations with ICI. My granddad could have charged the earth, but he only ever wanted to be paid a fair day’s pay for a fair day’s work. His clients respected him for that.”

Transforming a green goddess
SR Walton was the perfect person to thrive in an industry still in its infancy. The innovation he showed in the brewing industry stood him in good stead developing water jetting for petrochemical clients.
Initially the small trolley-mounted Mueller and Aldrich pumps were transported in Ward cattle trailers pulled by Land-Rovers.
“After several hair-raising incidents with the Land-Rovers and trailers, my dad and uncle Bill decided trucks were a better option and set about buying ex-military vehicles.
“We had Green Goddess fire engines from military auctions, the same vehicles that became famous in the firefighters strikes of the 1980s. They removed the fire pumps and kitted them out as water jetting platforms.”

Water jetting became crucial to the success of the UK petrochemical industry as it grew rapidly in the 1960s and 70s.
In the early 1960s the most popular water jetting pumps in the North East of England were supplied by Mueller. “Which is where the name for the jetting hoses came from,” said Richard Walton. “A bit like Hoover and vacuum cleaners. Even today, the old hands amongst us call them Muellers.”
Drawing on new designs
Douglas was also making full use of his technical drawing skills, learned as a young draughtsman at Dorman Long. He drew many of the diagrams used to illustrate the power and capability of this new water jetting equipment and designed the mole logo synonymous with the company.
With the water jetting industry developing fast, every contractor was looking to gain an advantage over its rivals. In the 1970s, Walton Mole believed it had done just that by being the first to import the new RBT 200 water jetting pumps from the USA.


It could deliver flow rates up to 23 gallons per minute and pressures up to 12,000 pounds per square inch, or 827 bar. Its four-speed gear box allowed water jetting to be carried out with a range of flow to pressure ratios, greatly enhancing precision.
With distribution rights for the equipment, Walton Mole sold RBT 200s around the world, and some are still in use today.
Early water jetting robotics
Walton Mole continued to innovate, swapping the General Motors engines that powered the pump with a Rolls Royce C6 NFL diesel engine. The company also made its own jetting equipment and nozzles, as other contractors were doing.
This was essential. From the 1960s onwards, operating pressures for water jetting equipment climbed continuously. By the 1970s they had reached 1500 bar, over 20,000 psi. There was no way technology could stand still.
Douglas, known as Doug or Dougie to friends and colleagues, was an excellent engineer, just like his father. He led the development of new water jetting systems, including a ‘bundle blaster’, an early example of a robotic jetting system.

A dirty heat exchanger could be placed in the 30ft-long steel container allowing its exterior to be cleaned with water jets mounted on a track. The jets could be rotated to achieve a far better clean than was possible with a hand-held lance.
Flight to the North Sea
It was a forerunner of semi-automated systems that continue to be developed to provide safer and more effective operation today. By the 1970s, Walton Mole was also very active as a contractor in the North Sea oil and gas industry – something Richard Walton remembers vividly.

“Our water jetting operatives could be working on oil rigs, or off supply barges,” he recalled. “To facilitate movement of supplies, wages and crews my dad would often be flown up in charter planes from Teesside Airport and he’d let my brother and me come along for the ride.
“Walton Mole also developed new equipment needed to support water jetting in the offshore oil fields. It included a ‘Koala’ water jetting system for the BP Forties oilfield, developed to clean riser pipes below the water line. The Walton Mole engineering team initially tested the device in a giant tank in the company yard before sending it to Scotland.
“For a 10-year-old lad, it was an amazing experience. We landed at Dundee airport once with essential equipment supplies and wages. These were then dispatched by taxi to a waiting supply barge going out to the Forties Field.
“On another occasion, I was excused from school on a Friday afternoon by my mum. She then drove me up to Montrose with my brother, David, and brother-in-law Richard to meet the Tender Commander, at the time one of the largest supply barges in the world.
“The ship was on contract to BP for Walton Mole’s Koala cleaning, shot blasting and painting project. We had essential gear sprockets for the Koala. Before the Tender Commander sailed on the Saturday morning high tide – we had a full tour of the supply barge. I remember the American saturation divers on the barge showing us around their decompression chamber.
“Sadly, we had to go back to Teesside in the car as dad set sail again for Forties platforms. We did the flights and drives on numerous occasions during the 70s. It was a fantastic adventure for a young boy.”

Proud to be a WJA founder
By the late 1970s, the company was also seeking to set its own standard for water jetting quality and safety. Walton Mole had its own code of practice and was the first water jetting company to hold BS 5750 quality systems standard.
In 1980, it was one of the contractors invited to the inaugural meeting of what was then the Association of High-Pressure Water Jetting Contractors, later to become the Water Jetting Association.
“My dad approached working with the association with the same passion he showed with Walton Mole to the point that he sometimes got completely carried away,” said Richard Walton. “There was a time he was invited to be a guest speaker for the association at a British Hydromechanics Research Association conference in Stockholm.
“The time he was allocated was 20 minutes, then five minutes of questions. My dad was still going strong after an hour and 10 minutes. The other water jetting association representatives in attendance were left pulling their hair out.”
3rd and 4th generation of water jetters
Imbued by Walton Mole’s engineering success and excitement, Richard Walton chose to take his father’s path and joined the family firm in 1984: “I had a phenomenal apprenticeship, through my dad, Uncle Bill, Mike, Dave, Brian, Mac and a whole host of other Walton Mole employees. Although the work was extremely tough at times, I wouldn’t have changed it for the world.”

In 1992, Douglas ‘Dougie’ Walton took early retirement due to problems with ill-health and appointed a manager to run the business. It turned out not to be a positive step. Walton Mole went into receivership in 1995.
“It was a sad end, really, for a company that was one of the founders of the water jetting industry in the UK,” said Richard Walton. “But Walton Mole’s legacy lives on. A lot of ex ‘Moleys’ are still very active in the water jetting industry and doing great things with other businesses. I do believe the spirit of SR, Douglas and Bill will live on for many years to come.”