Supersonic water jets boost highway improvement project
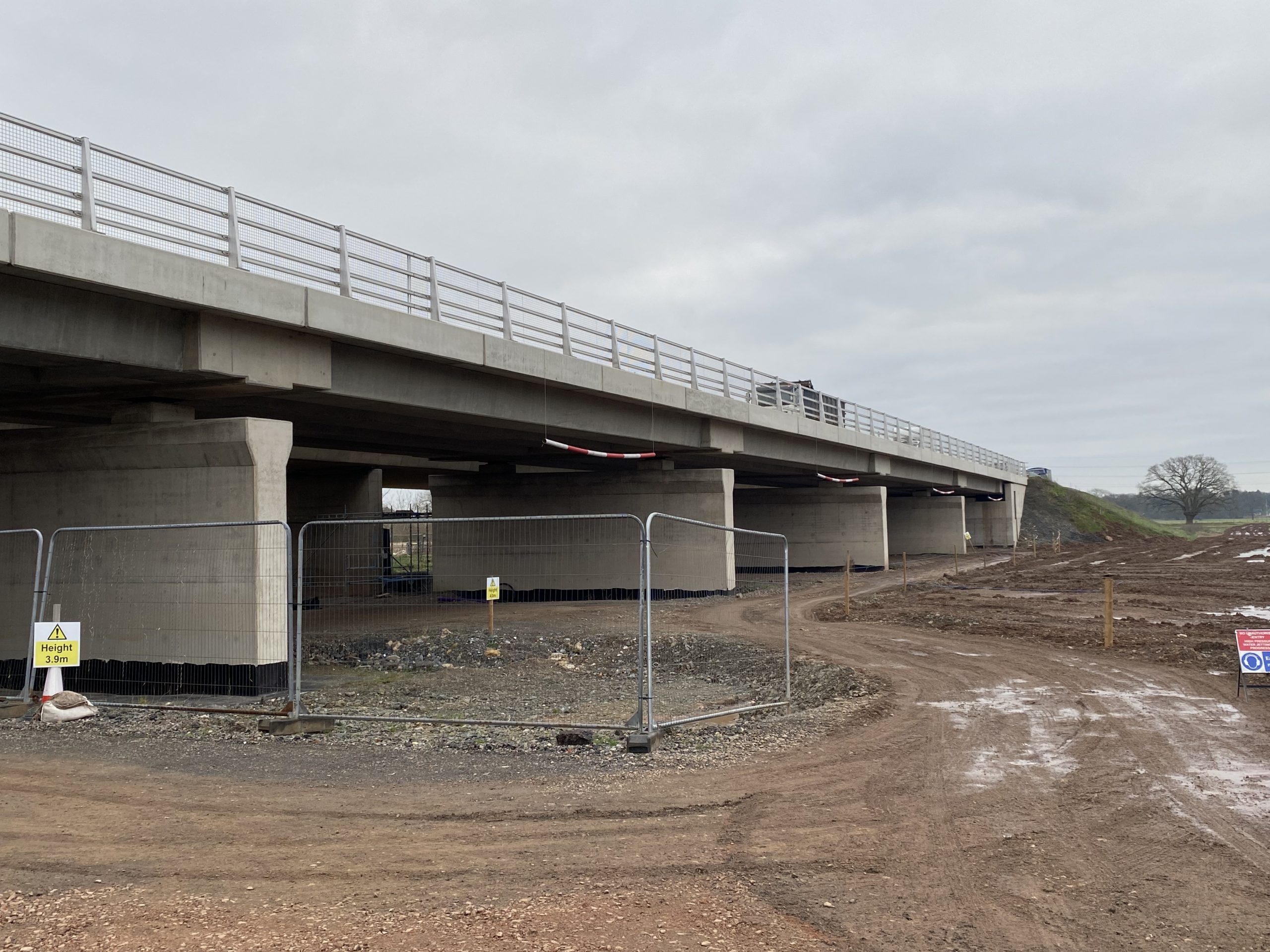
The destructive power of water is playing a key role in a highway improvement project along one of the busiest roads in the West Midland region.
Jets of water travelling at supersonic speeds are blasting concrete from around bearings in two flyovers on the A4440 Southern Link Road near Worcester.
The jets are so powerful that they can tear lumps of concrete bigger than a fist from around the bearings, exposing the steel rebar for the first time since the carriageway was built.
However, in the hands of the experienced operatives from hydrodemolition specialist Aquaforce Concrete Services, they can also be directed with impressive precision to remove just the right amount material.
Aquaforce is working on the project for its parent company, civil and structural engineering specialist Freyssinet, which is carrying out concrete repairs on the existing roadway on behalf of main contractor Alun Griffiths (Contractors) Ltd.
Worcestershire County Council is overseeing the £62m scheme to upgrade a 3.5-mile section of the link road connecting the M5 with south and west Worcester, Great Malvern, Ledbury, Upton and Herefordshire.
The project, now nearing completion, has involved the phased dualling of the carriageway and the repair and upgrading of the in situ roadway, including two raised sections over the River Severn and its flood plain.
Aquaforce, a member of the Water Jetting Association, has been working with Freyssinet to release 56 bearings on four abutments and 10 piers along the two flyover sections, so they can be released and replaced.

Freyssinet engineers jack up the carriageway to unload the bearing. Aquaforce operatives remove the concrete. The bearing can be removed. Concrete is reinstated, and a new bearing installed.
Their success demonstrates the advantages of hydrodemolition in supporting highway maintenance tasks, said Aquaforce General Manager Gavin Thomas, a member of the WJA’s technical committee.
He added: “Our operatives are exposed to almost none of the hand arm vibration (HAV) risks of mechanical tools, and water jetting causes no vibration damage to the structures we work on.
“Particles released are held within water, so dust pollution and highway visibility hazards are reduced. Also, structures like rebar are not damaged and surfaces need little or no further preparation before being reworked.”

The hydrodemolition is being carried out within encapsulated scaffolding to contain the thousands of shards of concrete ripped from structures by the water jet.
Aquaforce is using trailer-mounted high pressure water pumps supplied by Calder, also a WJA member, manufactured just down the road from the A4440 worksite, on Worcester’s northern outskirts.
Its operatives’ handheld jetting guns are set at an average pressure of 1100 bar (17,000 psi) and a water flowrate of 48 litres per minute.
The 10m3 of water needed by each team every shift is collected by an Aquaforce tanker from a nearby standpipe and delivered to site.
Wastewater is filtered to remove a significant percentage of suspended solids and pH balanced on site to ensure it can be disposed of safely and correctly.
Each abutment and pier has four bearings. On average, one bearing can be undermined ready to be released every shift, a task that involves removing approximately one metre cube of concrete.
It is a level of productivity that no other methodology is likely to match, which is why hydrodemolition has become the standard method to release bridge bearings in the UK.
A key consideration throughout has been safety. Supported by the WJA’s blue code of practice for high and ultra-high pressure water jetting, hydrodemolition has an excellent safety record.
However, the enormous power of water jets, which can reach operational pressures greater than 2,700 bar (40,000 psi), means there is no room for complacency.
Aquaforce’s operatives wear the latest water jetting suits made from the same material used in bulletproof vests and suits worn by bomb disposal technicians.

Steel lined boots, and helmets with visors that have to be regularly replaced because of the battering they take from concrete shards, complete the specialist PPE.
Training is also central to maintaining safety and quality standards. The WJA is the main provider of water jetting training in the UK.
Its class-based safety awareness course and practice modules, accredited by City & Guilds, are designed to give operatives the fundamental knowledge and skills they need to begin their water jetting careers.
To maintain WJA registration, safety awareness must be refreshed every three years. Now operatives and their employers can benefit from a new WJA course, the world’s first competency qualification for water jetting.
Accredited by ABBE, the Level 2 Water Jetting Technician Certificate, adds a substantial period of work-based assessment (at least a year) carried out by a WJA-approved assessor, to establish that operatives have a higher level of understanding embedded in operational behaviour.
WJA Training and Safety Committee Chairman Darren Hamilton said: “Our Level 2 certificate is designed to support all those involved in the water jetting process, the operatives, their employers and clients.
“Operatives can be more confident they are following best practice. Employers are supported in building and retaining skilled and motivated teams. And clients will have greater assurance on safety and quality.”
In its latest initiative, the WJA is seeking to support high pressure washing standards with the introduction, in 2022, of a new code of practice for pressure washing.
Named the ‘Purple Code’ thanks to its purple cover and will, it will set out best practice for low pressure water jetting procedures and support learning in the WJA’s pressure washing training course. Darren Hamilton said: “We’re expecting construction contractors, who use pressure washing widely, to welcome our code of practice, which will help underpin safety and operational performance.”